The most common monofilament fiber is made of high-molecular-weight polypropylene. This material is relatively inexpensive and easy to extrude. It also has good linear strength and good wear resistance, which are important for industrial applications. Its two-phase polymer morphology is also desirable for monofilament applications.
High-tenacity monofilament yarns are used in tire cord fabrics and UV-protected fabrics. High-tenacity monofilament yarns are available in various deniers. They can range from 840D/140F to 1680D/280F.
High-tenacity monofilament yarns are produced using a method that includes melting and orienting a thermoplastic elastomer. This method also includes a dynamic annealing step. This process imparts reduced elongation and shrinkage to monofilament fibers. This allows for more effective thermoplastic elastomer use in industrial fabrics.
High-tenacity yarns have a tenacity of 60 to 85 cN/tex. They have an elongation at break of 15% to 35% and a low hot air shrinkage of 4 to 10%. In addition to a wide range of uses, high-tenacity yarns are also used in airbag fabrics.
High-tenacity monofilament yarns are commonly made of polyethylene. They have a low water absorption rate and can resist chemicals and fuels. They also have excellent stiffness and mechanical strength at low temperatures. These properties make them ideal for filtration fabrics.
The single filaments can be twisted to form ply yarns, cords, and ropes. They are also capable of being twisted into a variety of different shapes. Typically, the twisted filaments are twisted in alternating directions to form a rope or cord.
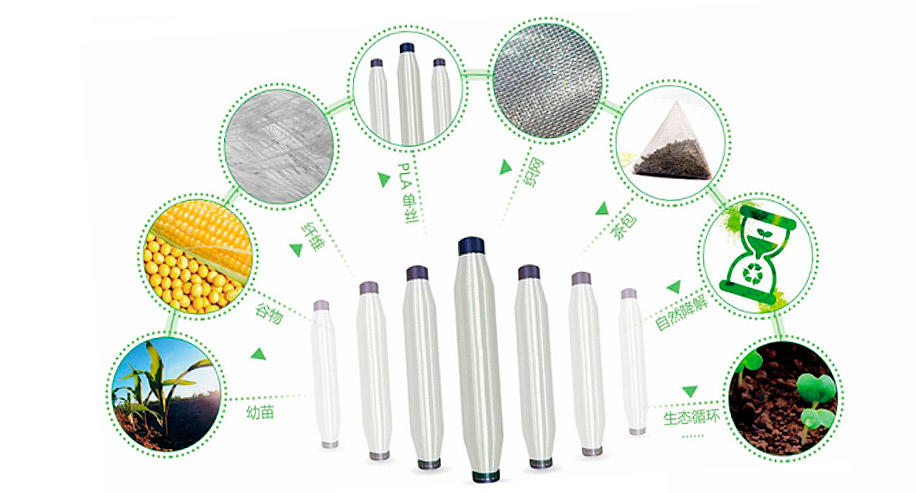