Polypropylene is a common monofilament fiber. It is inexpensive, easily extruded, and has high linear strength. The extrusion temperature for polypropylene is typically between 190 and 200 degrees Celsius. However, temperatures higher than this lower the melt viscosity. Nylon polymers are used for selective monofilament applications. Their cost is disproportionate to their benefits, so they are usually used only where certain properties are needed.
To determine the compatibility of PET and PTT in the production of PET composite monofilament, preliminary XPS analysis was performed at the ICMATE-CNR, Padova, Italy. The three types of PET sheets were characterized under different d.c. conditions. Although the difference between the coatings was not clear, the percentage of carbon and oxygen in each of them increased as power increased. Nitrogen content decreased significantly in the treated sheets, but was not as pronounced as in untreated sheets.
In addition to its flexibility, PET Composite Monofilament offers excellent chemical compatibility. Depending on the application, it is an ideal choice for 3D printing filaments. Its low weight and environmental-friendly properties make it an ideal candidate for applications where dimensional stability is critical. The fineness of the fiber is important for various processes, including the extrusion process. With the right mixture of polyethylene terephthalate and nylon, the resultant product will be strong and versatile.
The melting of PET is essential for the final product. It is also important to control the denier of the PET monofilament. The melting of PET has to be controlled carefully to prevent the product from becoming unstable. The resulting composite material will be resistant to both hot air and water. Once a product is cooled to room temperature, it will not melt. This is an essential characteristic for a PET polymer.
After the polymer is formed, it is spun onto individual spools or tubes. These spools are arranged in a row or bank. Each winder is controlled by a tension feedback device. The spools are manually changed when the end is filled. Automatic transfer winders are available in the market. The speed of the PET fiber extrusion process makes it an ideal option for small manufacturing.
During the process of spinning PET composite monofilament, the fibers must be quenched. The large diameter polymer fibers are quenched in water baths while the smaller diameter ones are quenched in air chambers. The speed of the rolls is controlled by the diameter of the polymer. It is also important to check the thickness of the filaments to ensure that they are uniform in diameter. This is very important as the filaments must be consistent to ensure durability.
After a PET composite monofilament is produced, the facing of the filaments must be carefully controlled to avoid melting and separating. The melting process is a complex process, which must be carefully monitored. This process is known as the "splitting" process. It involves the mixing of the two phases. The polymer is then spun on the filaments. The resulting products can be used in a wide range of industries, including plastics.
After plasma treatment, samples were vulcanized using the same sheet of compound. The polymer faces were then exposed to the polymer facing for several months. The resulting PET composite monofilament has a high tensile strength. The PET component also contributes to the uniformity of the fibers, which is essential in thermoplastic materials. They are ideal for composites and are used for medical applications.
The PPOL coating on PET monofilament is highly sensitive to heat. The polymer coating is very sensitive to the heat and moisture. Its tensile strength is dependent on its temperature, and the melting temperature of the facing is important to determine its strength. This is why thermoplastic materials are a good choice for many applications. They are flexible and have low weight. You can also use them in aerospace.
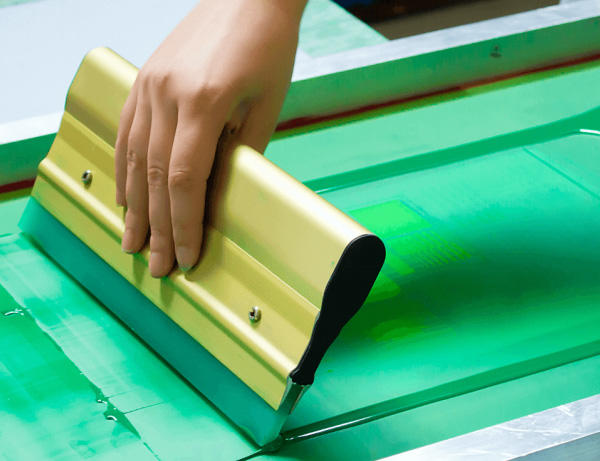