The manufacturing process of the present invention enables production of industrial monofilaments with a fine central channel that is substantially uniform in diameter and concentric along the axis of the filament. This type of monofilament is much improved over existing products, achieving nearly the same tensile strength as the ideal solid monofilament. In addition, the cross section of this new product is considerably larger than known monofilaments.
During the first stage of processing, the monofilament is stretched to a relatively high tensile strength. It is then drawn into a bath of water at a temperature of about 20 C. to 40 C. This causes a rapid cooling, which causes hollow spaces to form. The size of these hollow spaces is dependent on the diameter of the monofilament. They can vary within prescribed limits of the hollow channel cross section.
The hollow channel of the monofilament is then partly stretched in the bath, through a suitable regulation of the rate of withdrawal. This leads to a gradual reduction in the outer and inner diameters. The final reduced diameter is generally less than one-half of the value of the outer diameter at the spinning nozzle. The extent of the stretching is determined by the type of thermoplastic polymer and the degree of stretching desired. The preferred reduction is one-half. This serves as an upper limit for the total outer and inner diameters.
The second stage of the manufacturing process involves reducing the size of the fine concentric channel of the monofilament, so that it reaches a relatively small percentage of the overall cross section. This is done by drawing the monofilament into an aqueous cooling bath at an interval of about 60 mm. It is then drawn upwardly out of the bath. This process is repeated until the outer and inner diameters are sufficiently reduced to produce the desired product.
This new process is effective at producing industrial monofilament without the need for special apparatus, or for specific knowledge of the conditions under which the polymer is being processed. It allows a very quick turnaround, and is also able to avoid defects on the surface of the product. This ensures that the loading capacity is high.
A second series of rolls is then used to increase the speed of the filament by four to seven times. The speed of the winders is individually controlled by a tension feedback device. This is an important step because it is the fastest way to achieve a large loading capacity.
The final product of the manufacturing process is then wound on individual spools, and packaged for shipping. This type of product is used in a wide range of applications, including toothbrush bristles and fishing line. Currently, the market for industrial monofilament is primarily segmented into North America, Europe, Asia Pacific and Middle East and Africa. Increasing demand for medical and automotive industries in these regions should help fuel the growth of the monofilament market.
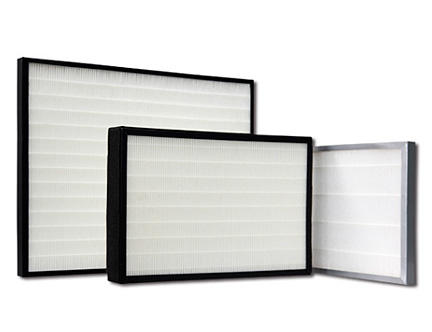