The process of manufacturing a PE monofilament yarn is similar to other fiber spinning processes. After melting, the polymer is extruded through tiny holes on the spinneret. The size of the holes determines the strength of the filament. The diameter of the fiber is the determining factor for the extrusion speed. The polymer is then filtered through a spin pack before being spun into a filament.
The filaments are then drawn and cooled. They are then packaged and sent to customers. The filaments are dope dyed if desired. They are then tested for their properties. They are available in different shapes. The most common is a diamond shape. The S shape and the U shape are also common. They are softer and have more natural looking appearances.
The polymers used for monofilament fibers are typically low density and medium density PE. Both types of polyester can be twisted for different lengths. They are commonly used in selective monofilament applications. The two resins have a range of linear weights, 6,000 to 63,000 deniers. The final diameter of the filaments is determined by the density of the main chain. The larger the diameter, the slower the extrusion speed. The thinner the diameter, the higher the speed.
The fibers are tested for tensile strength and abrasion resistance. They were compared to polyamide and PVC-based polyesters. The results showed that PET polyamides were better than the PVC-based polyesters. The tensile strength was 6.9 to 7.7 g/den. The abrasion resistance was 100 kLy.
PET polymer monofilament yarns are ideal for woven fabric and nonwoven applications. They are more durable than PVC, and can withstand UV rays. They are less flexible than polypropylene. Their abrasion resistance makes them suitable for sports surfaces. They are available in a wide variety of colors. They have been successfully applied in a wide variety of applications, including weed-eater string, anti-bird nets, weaving, and more. They are also useful for faxes, fishing nets, and geotextiles. They are also used to produce fabrics for building houses, lining garments, and more. They are also suitable for weaving and knitting.
In contrast to nylon, polypropylene has a lower melting point and is relatively inexpensive. Polypropylene is also easy to extrude. The extrusion temperature for polypropylene is in the range of 190 degC. It is also a good choice for sports fields because its low density allows it to float in water.
Polypropylene monofilament yarn is very strong and is easy to handle. It has high tensile strength and high elasticity. They can be used for woven fabrics, nonwoven fabrics, and sports surfaces. They can also be used to make mesh bath sponges. They are less flexible than polypropylene, but they have a high abrasion resistance. They are a popular choice for synthetic turf products.
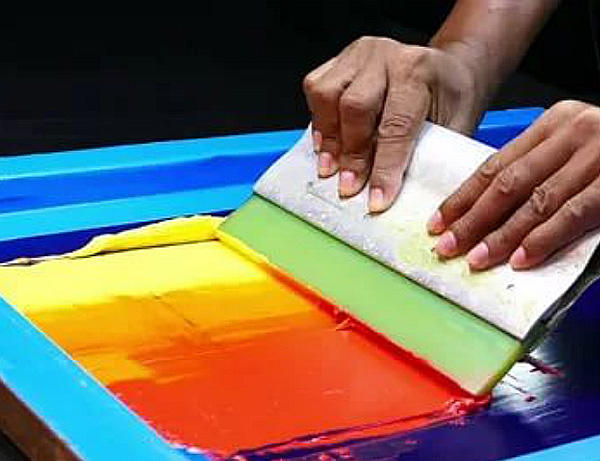