Monofilaments are manufactured using two basic steps. First, they are heated and cooled. Large diameter filaments are usually quenched in a water bath, while small diameter fibers are quenched in air chambers. The diameter of the filaments determines the speed of the extrusion process. Larger monofilament typically requires a lower extrusion speed than small monofilament.
This mixture is then processed using a single-screw extruder. The resulting melt is spun through a 0.8 mm spinneret, and the screw temperature is 240 to 270 degC. The screw speed is 22 m/min. The resulting melt is then processed into monofilaments by a three-stage draw process. The water bath temperature is 98degC, and the draw ratio is 8.5. After the melt is spun through the first two steps, the alloy is processed to a monofilament of the desired diameter, with a line density of 35.7 to 40.3 tex.
PP monofilaments have a high linear density and are sturdier than multifilament fibers. This material is commonly used for belts, ropes, hawsers, and mooring cables. It also has a high shear strength, making it an excellent choice for applications where it is necessary to have a consistent diameter.
HDPE monofilament is an ideal starting material for weaving, braiding, and twisting. They also have a large color spectrum.
Polyethylene is the most widely used plastic in the world. It is made up of long chains of carbon atoms with two hydrogen atoms attached to each carbon atom. The molecules of polyethylene are complex and some are branched. This type of polyethylene is more dense and stronger than linear polyethylene.
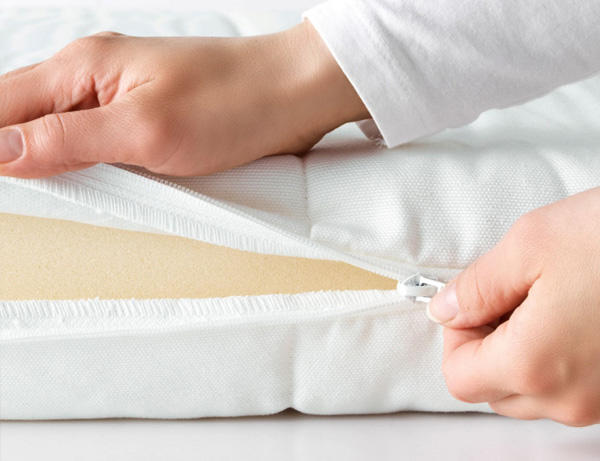