The polyester multifilament yarns of the present invention have an elongation at break of 12% or more and exhibit a high workability. They have an excellent breaking strength of 4.5-45 MPa or less, which allows for adequate mechanical properties even in thin fabrics.
A high degree of interlacing results in large binding points and reduces the abrasion resistance and durability of the fabric. The preferred level of interlacing is 15.0 pieces/m. Higher levels of interlacing may increase the number of defects, resulting in yarn breakage.
A method to obtain a polyester multifilament yarn is similar to that used in example 9, except that the core component is PET with an intrinsic viscosity of 1.25. Spinners set the interlacement position before drawing spun yarn. Warp yarn breakage was a common problem during weaving with polyester multifilament yarn, and a technique called "stopping every m" may lead to more filaments breaking apart than the two-step method.
The polyester multifilament yarn of the present invention has a total fineness of four to 30 dtex and a single-fiber fineness of 1.0 to 5.0 dtex. The breaking strength of the polyester multifilament yarn is 5.0 to 9.0cN/tex, while the elongation at break is 12 to 45%. The degree of interlacing of the polyester multifilament yarn is between two and fifteen pieces/m.
Another method of manufacturing polyester multifilament yarn is to combine polyester yarns with an inorganic particle called titanium oxide. Titanium oxide adds strength to polyester multifilament yarn and is added to the polyester polymer in amounts ranging from 0.1 to 0.5 wt%.
The most common monofilament fiber is polypropylene. It has low cost, is easy to extrude, and has high linear strength. It is a good choice for lining garments, as it reduces the likelihood of snags and wear. Moreover, it helps reduce the risk of garments ending up in landfills.
Polymers are heated to crystallize and heat-stabilize before they are drawn out into monofilament yarns. This process requires the filaments to be stretched several times and then drawn out with a special tool called a comb guide. The filaments then exit the oven at a lower speed than the draw rolls, reducing tension in the filaments and resulting in a finished yarn.
Abrasion resistance is a key issue in improving the performance of woven fabrics in advanced applications. While yarns with abrasion resistance have great advantages, they also have the potential to break or be ruined by friction.
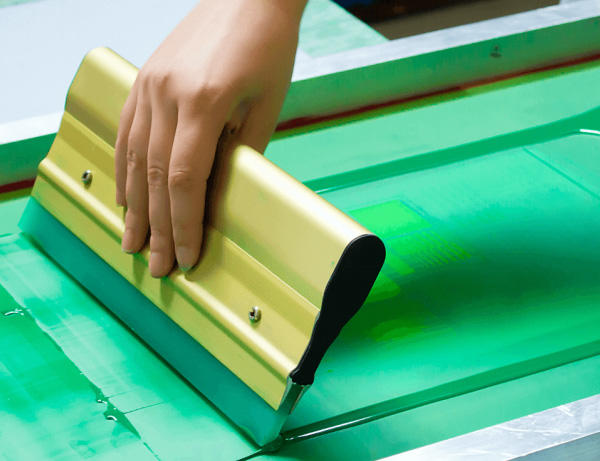