The process of producing polyethylene monofilament yarn begins with a process that requires the filaments to be stretched to a high strength level. This process is then followed by the winding of the filaments onto individual tubes or spools. In some cases, filaments are arranged on a single row or bank of rolls. In either case, the winders are controlled by a tension feedback device. Although automatic transfer winders are available in the market, their use is not justified due to the low processing speed of monofilament lines. The filaments are then tested for properties and packaged for shipment.
In addition to these applications, monofilament yarns are also found in everyday life. Some examples are fishing lines, zippers, hook-and-loop fasteners, and belts. Monofilament yarns are also used in household appliances and filters. You may even have seen them in a treadmill walking belt.
Monofilament yarns are often used in construction to protect plants from insects and debris. Some construction companies also use them to cover falling objects. Monofilament fabric is also used in Jakarta, where it covered a river as part of a project to beautify the city for the Asian Games.
A single-stage, compact process combines all the production steps, and is generally more economical for small-scale production. The spinning stage can reach speeds of 100-300 m/s. Grid-structured spinnerets are another important feature of this process, as they allow for faster spinning. The filaments produced during this stage are then woven together into a tow. The tow is then fed continuously to the drawing unit. The resulting yarn is used in carpet yarns and non-woven products.
Another application for polyethylene monofilament is insect net. These mesh fabrics are made of polyethylene and contain anti-aging and anti-ultraviolet additives. These fabrics are effective at preventing common insects like mosquitoes and flies. They can also be collected easily.
The next step in polyethylene monofilament fiber production is to cool the filaments. Large diameter filaments are usually quenched in a water bath, while smaller diameter fibers can be quenched in an air chamber. Extrusion speeds depend on the fiber diameter. Larger diameter polyethylene monofilament fibers are extruded at slower speeds than smaller diameters.
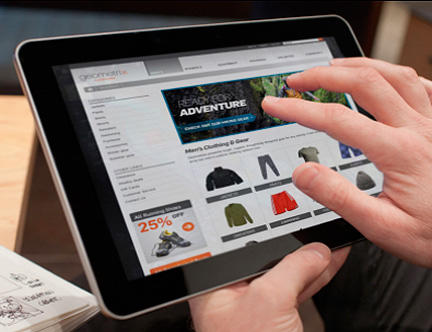